Snow and ice control
Snow removal and de-icing is arguably the most crucial, yet challenging responsibility of the our highway department. We strive to maintain safe driving conditions, both in clearing the snow and applying de-icing material. We also must balance the devastating, cumulative effect road salt has on our infrastructure, lakes, groundwater, and surrounding vegetation. Many factors and much thought goes into every decision to deploy our plow trucks.
Fremont Township is responsible for the removal of snow and ice on 45 centerline miles of road, including 53 cul-de-sacs. While our goal will be to have all areas cleared “curb to curb” within 12 hours of the end of an event, limited staffing may preclude that during prolonged events. Our emphasis will be on making sure all areas are cleared to allow passage of emergency vehicles, delaying a complete clean-up until our drivers have received adequate rest to perform safely.
CREW
Our plowing crew includes 5 full-time highway employees, 2 park employees, and the highway commissioner. With 7 routes to cover and 8 drivers, we are unable to have split shifts and 24 hour coverage. Whenever possible, we limit duty time to 12 hours. However, during prolonged snow events, our crew may split into 2 smaller crews of 16 hours of duty and 8 hours of rest.
Equipment
Our department runs a fleet of 7 plow trucks. Plow lengths vary from 9-12’. 3 trucks are equipped with side mounted wing blades. All trucks are equipped with an automatic controller that regulates the amount of salt emitted, as well as liquid tanks and dispersing system for pre-wetting the salt. Liquid capacity varies from 35-300 gallons.

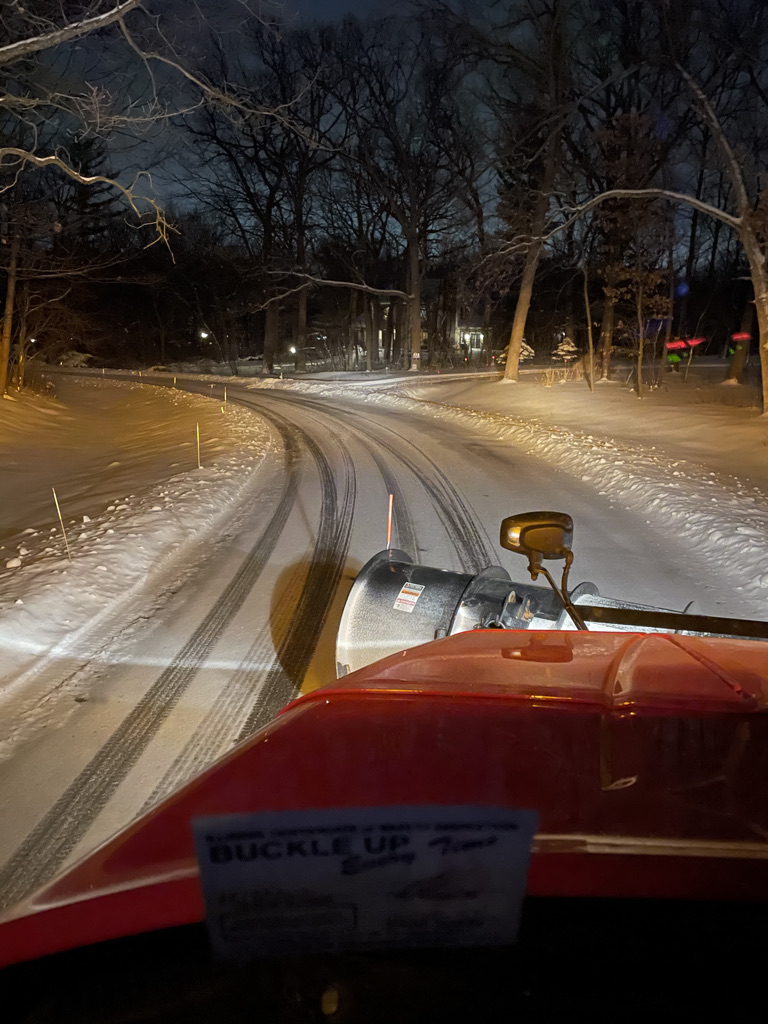
De-icing Material
De-icing materials will not be used to melt snow. Drivers must first plow all surfaces and then add salt and liquid to prevent refreezing of pavement.
Prior to dispersal, the salt is pre-wet with a liquid blend of calcium chloride brine enhanced with organic compounds. Pre-wetting the salt reduces the amount of salt needed, speeds up the melting process, and minimizes salt bouncing off the road. The liquid gives the salt a brownish hue and a vinegary smell.
- 400 lbs per lane mile and 20 gallons of liquid is our standard application while salting.
- 250 lbs per lane mile and 15 gallons of liquid may be used during minor events when a warm-up is forecasted.
Timing our Plow Routes
While no two storms are handled the same, there are some consistencies with the timing of our plow routes. Whenever possible, our department will avoid plowing during the am or pm rush hour and between the hours of 10pm-3 am. For overnight snow falls, our crew will typically start their plow routes at 3 am, with a desired completion time of 6am. If subsequent plowing is needed, we wait a minimum of 3 hours (if snowfall rate allows) to give salt from the prior round time to take effect. For most storms, evening rounds will end by 10pm to allow for our crew to rest before the morning round.
ACTIVATION
Every snow/ice event is unique and each one is evaluated for considerations, such as current temp and forecasted temp, type of precipitation, amount, duration, winds. With amounts less than 1” and a forecasted warm-up above freezing, our crew will focus on clearing and salting the arterial roads and areas that have hills where stopping for an intersection is a concern. The same 1” of snow with below freezing temps forecasted will necessitate covering all of our roads. With snow falls of 5” or more when multiple rounds are expected, our crew will wait until 3 or more inches have fallen before starting on their first round. In most circumstances, subsequent rounds will not be initiated before 3 hours since prior salting to allow time for salt to take affect.
When more than one round is expected during a snow event, it is common for our crew to complete one pass through all areas without doing a complete clearing of cul-de-sacs. Cul-de-sacs are very time consuming to clear, so whenever possible, our department will save the thorough cul-de-sac cleaning until the final round.
No parking on roads
When there is a reasonable chance of snow, please do not park on township roads. Some areas become impassible with our plow trucks, greatly affecting our ability to remove snow and adding substantial time to our routes. This is also in the best interest of your vehicles, both with salt spray and the risk of slipping in icy conditions.
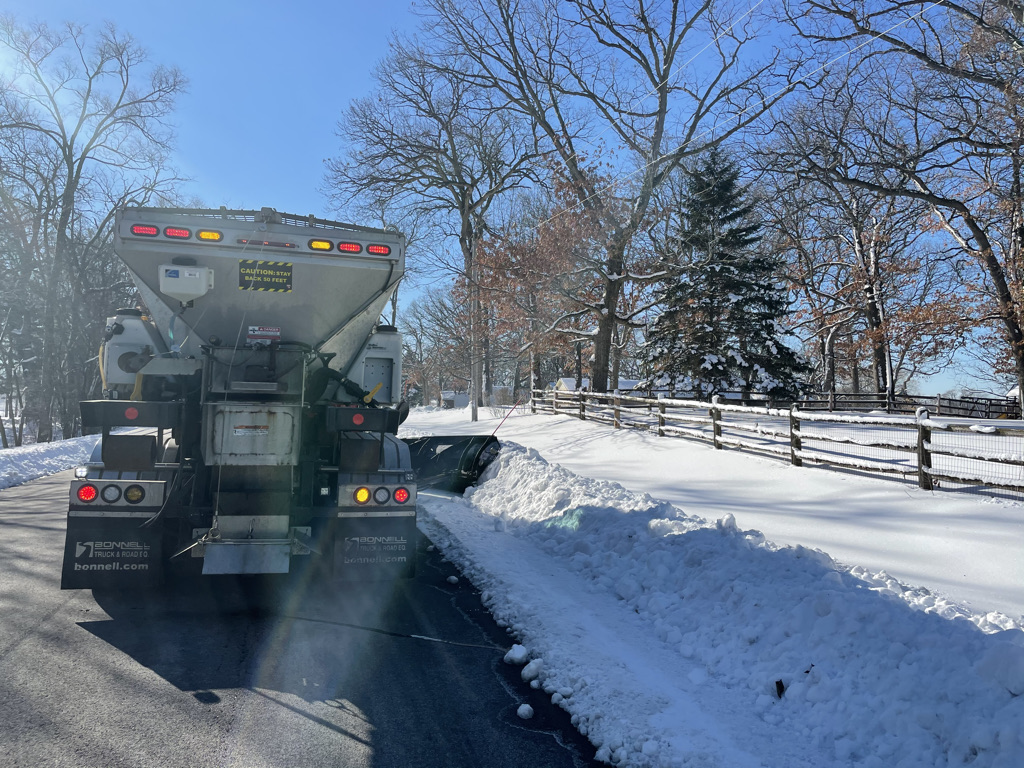
Creating shoulder snow space
As snow quantities grow along the shoulder or curb, our trucks equipped with wings will push back the snow to create space for future snowfall. In some areas, we may deploy a wheel loader to move snow piles to improve visibility or maneuverability around intersections.
Shoveling snow into road
Shoveling snow, ice or any material onto a public road is unlawful. Please do not push your snow across the road and into your neighbor’s property.
Damaged Mailboxes
Many of our mailbox damages are due to the weight of heavy snow coming off the plow. Please ensure your mailbox post and base are in good condition to withstand the forces of snow. We will not replace rotting posts or base, although we will attempt to repair or put a temporary mailbox in place.
If your mailbox is damaged during a plowing event, please email or call our highway department, and we will repair or replace. Please note that replacements will be a standard 4x4 cedar tone post and a standard mailbox.
To report a damaged mailbox:
Plow Damage
In the spring, when snowfall season is likely over, our crew will begin fixing damage to turf from the plows. We will pick up any clumps of turf displaced by our operation, followed by adding topsoil/grass seed/straw blanket as needed.
FAQs
Why does the plow leave a pile of snow at the end of my drive? Can you clear it for me?
As the snow quantities build on the shoulder, the plow carries more snow with it until it reaches an area with less snow (your driveway), and snow rolls off the plow and fills the space. It’s impractical for our drivers to try to re-direct the snow away from the hundreds of driveways they pass with each round. We do look for opportunities to unload the plow as much as we can prior to reach driveways, although we have limited options in many cases. We unfortunately cannot clear the end of your driveway as our efforts are needed to maintain public roadways.
Why do you avoid plowing during rush hour?
Many of our roads intersect with busy state and county roads. During rush hours, clearing these intersections can be more hazardous for our drivers and you.
Why are some roads white with snow/ice and others are black?
The effectiveness of our snow removal operation depends on temperature, sun exposure, asphalt quality and traffic amounts. More traffic works the salt into the snow/ice, speeding up the melting process. A blue sky, sunny day of single digits can melt snow on the roads, while a cloudy, dark day of upper 20s may see little melting.
What are the limitations of salt?
The minimum practical application range for salt is a pavement temperature of 15-20° F and above. While salt will melt snow and ice down to a pavement temperature of -6° F, it can melt over five times as much ice at 30° F as at 20° F. Thus the effectiveness of salt is sensitive to small differences in pavement temperature. Snowplow operators attempt to apply only the amount required for temperature, time and use, too little and the roadway will refreeze, too much is a waste of money and resources.
When the pavement temperature drops below 15° F the effectiveness of salt is decreased significantly. At lower temperatures MnDOT will begin adding other chemicals to the salt such as calcium chloride or magnesium chloride that will lower the freezing point even further.
Wind conditions must also be considered when deciding to apply salt or other chemicals to the roadway. As temperatures drop and the snow becomes dryer, snow blowing across the pavement will stick wherever there is chemical present. This can create a hazardous condition that would not have existed if no deicing chemical had been applied.
The effectiveness of salt can also be affected by the pavement type. Salt works better on new asphalt (blacktop) than on concrete pavements.
In order to reduce salt bounce and scatter and to help it adhere to the pavement, salt brine or other liquid deicers are sprayed on the salt at the spinner on the back of the truck. This is called pre-wetting. This strategy helps to reduce the overall amount of salt needed to return the roads to safe winter driving conditions. Pre-wetting also helps to jump-start the melting process, making the salt work more quickly.
How much salt does your department use in a season?
In 2020, we used 450 tons of salt. In 2019 with minimal snow fall but several icing events, we used under 400. Prior to upgrading our dispersal equipment and limiting our rounds, our totals were significantly higher. Our salt costs betwen $60-80/ton, which doesn't seem like alot, until you factor in the costs to our infrastructure from its corrosive strength. Studies have estimated that the true cost of salt is 10-20x times the purchase price.